Al automatizar los procesos de back-end, las empresas de semiconductores pueden maximizar el impacto al optimizar los sistemas operativos, las palancas de gestión, las mentalidades y los comportamientos.
La industria de los semiconductores tiene una reputación de fabricación altamente técnica y ultraeficiente, lo que aparentemente ofrece un modelo para operaciones de vanguardia.
Sin embargo, esta percepción puede fallar en un área.
A pesar de proporcionar la inteligencia para la economía digital, las empresas de semiconductores a menudo van a la zaga de otras industrias en automatización y transformación digital, especialmente en actividades de back-end, que implican cortar obleas en chips individuales, procesos de prueba y empaque.
juego para los fabricantes de chipsCompartir
Cómo la automatización de back-end puede cambiar el juego para los fabricantes de chips
18 de agosto de 2023| ArtículoCompartir
AhorrarAl automatizar los procesos de back-end, las empresas de semiconductores pueden maximizar el impacto al optimizar los sistemas operativos, las palancas de gestión, las mentalidades y los comportamientos.
La industria de los semiconductores tiene una reputación de fabricación altamente técnica y ultraeficiente, lo que aparentemente ofrece un modelo para operaciones de vanguardia. Sin embargo, esta percepción puede fallar en un área. A pesar de proporcionar la inteligencia para la economía digital, las empresas de semiconductores a menudo van a la zaga de otras industrias en automatización y transformación digital, especialmente en actividades de back-end, que implican cortar obleas en chips individuales, procesos de prueba y empaque.1barra lateral
Sobre los autores
La falta de automatización en las operaciones de back-end puede tener consecuencias importantes, ya que estas actividades suelen representar del 20 al 25 por ciento de los costos de fabricación. Las consecuencias podrían volverse más severas a medida que las empresas pasen a la próxima generación de empaques avanzados .2o si reubican la fabricación más cerca de casa, a menudo en países con costos más altos, como muchas empresas están considerando ahora.
Al aumentar la automatización de back-end, los fabricantes de dispositivos integrados (IDM) y los jugadores de ensamblaje y prueba subcontratados (OSAT) pueden aumentar significativamente la capacidad de rendimiento al tiempo que reducen o eliminan la necesidad de costosas expansiones de gastos de capital a largo plazo. La automatización también les daría a las empresas más visibilidad y control sobre las cadenas de suministro, y eficiencias de costos, lo que conduciría a mejoras proporcionales en el resultado final.
El estado actual de las operaciones de back-end
En la actualidad, solo el 30 % de las empresas de semiconductores implementan inteligencia artificial o aprendizaje automático a escala (Gráfico 1). Las razones, dicen los líderes de la industria, incluyen la falta de capacidades, preocupaciones sobre la seguridad de los datos, problemas técnicos y de conectividad y, a veces, casos comerciales poco claros.3
Exhibición 1
Incluso las empresas de semiconductores que han progresado en IA y aprendizaje automático (ML) todavía tienen muchas oportunidades para capturar valor adicional. Nuestra investigación muestra que AI/ML contribuye entre $ 5 mil millones y $ 8 mil millones a las ganancias anuales, antes de intereses e impuestos, en toda la industria. Si bien esta es una suma impresionante, refleja solo alrededor del 10 por ciento del potencial total de AI/ML. Además, las actividades con mayor probabilidad de beneficiarse de la creación de valor relacionada con la IA son la fabricación y la I+D, dos áreas en las que es posible que se apliquen menos.
Más recientemente, los desafíos de la industria en el piso de producción se destacaron durante la pandemia mundial. En medio de plazos de entrega que se extendían por seis meses o más, la escasez de chips provocó ralentizaciones en industrias que van desde la automotriz hasta la agrícola. Incluso ahora, a medida que disminuye el impacto de la pandemia, sigue habiendo escasez de chips en múltiples áreas, especialmente en aplicaciones cotidianas como automóviles, electrodomésticos, dispositivos médicos y productos electrónicos. Mientras tanto, el crecimiento de la fabricación será lento hasta al menos 2026, a pesar de las enormes asignaciones de fondos, la mayoría de las cuales se destinan a capacidades de front-end. En una industria que se prevé alcanzará $1 billón en ventas anuales para 2030,4hay mucho margen de mejora.
La automatización aumenta el rendimiento, el rendimiento y la productividad
Nuestra experiencia reciente trabajando con los principales IDM y OSAT muestra que una transformación de fabricación de back-end concertada puede producir importantes beneficios de rendimiento durante un período de 12 a 18 meses. Las transformaciones más exitosas adoptan un enfoque holístico, que cubre el potencial de efectividad general del equipo (OEE) (incluida la implementación digital y la automatización), la planificación en la planta, la coordinación de la cadena de suministro, el costo total de rendimiento y la calidad de salida (rendimiento, desechos y fallas) . Si se implementa de manera efectiva, la acción en estas áreas puede conducir a un aumento del 20 al 30 por ciento en el rendimiento del piso de producción , una disminución del 20 por ciento en los costos unitarios de producción y una disminución del 30 por ciento en las quejas de los clientes, todo con un gasto de capital neto cercano a cero.
Las claves para capturar los beneficios de rendimiento de back-end son la automatización y la innovación digital. En términos prácticos, esto se desarrollaría en múltiples aspectos de las operaciones. Sin embargo, un primer paso importante sería establecer una sala de control digital, un “puente en el barco” que facilitaría el análisis de los pasos del proceso de cuello de botella, como la molienda, la unión de cables/la fijación de la tapa, las pruebas o el quemado. El impacto de crear una visión general holística informada digitalmente puede impulsar la OEE hasta en un 20 por ciento. En un caso de uso, la optimización de los parámetros de prueba aprovechando lo digital y el análisis condujo a una reducción del 13 % en el tiempo de prueba (Anexo 2).
Anexo 2
We strive to provide individuals with disabilities equal access to our website. If you would like information about this content we will be happy to work with you. Please email us at: McKinsey_Website_Accessibility@mckinsey.com
Un hilo común que atraviesa estas experiencias es que los datos son el alma de una transformación exitosa, respaldan la optimización de principio a fin y garantizan que el mantenimiento, por ejemplo, de los controladores y evaluadores, sea oportuno y efectivo (Anexo 3). En un programa piloto, una empresa logró una reducción del 40 por ciento en el tiempo de inactividad mediante la introducción de procesos de mantenimiento predictivo. Otro desbloqueo basado en datos es RTD (despacho en tiempo real), que se puede vincular a una coordinación más amplia de la cadena de suministro. Además, los datos pueden informar a la gerencia sobre el desempeño del costo total, por ejemplo, en relación con las adquisiciones y la mano de obra.
Anexo 3
Nos esforzamos por proporcionar a las personas con discapacidades el mismo acceso a nuestro sitio web. Si desea información sobre este contenido, estaremos encantados de trabajar con usted. Envíenos un correo electrónico a:
McKinsey_Website_Accessibility@mckinsey.com
Tres áreas de enfoque que cambian el juego
Los mayores obstáculos para hacer operativos los cambios de back-end a menudo se encuentran en tres áreas comerciales distintas: sistemas operativos, sistemas de gestión y mentalidades y comportamientos. Las transformaciones exitosas casi inevitablemente tendrán en cuenta estos parámetros, con soluciones diseñadas para abordar puntos débiles específicos en el proceso de producción.
Sistemas operativos
Un desafío común es que las empresas no tienen la infraestructura para detectar o remediar las ineficiencias en las operaciones del taller. Por lo tanto, la transformación idealmente incorporaría capacidades avanzadas en el sistema operativo. Las mejoras incluirían técnicas de gestión visual, incluidos lotes con códigos de colores o ubicaciones de lotes en ubicaciones etiquetadas específicas. También incluirían rutinas de flujo de trabajo en curso y procedimientos operativos estándar (SOP) para monitorear los cambios y el desempeño del operador. Un factor que a menudo se pasa por alto es el diseño de la máquina, que debe optimizarse para reducir los tiempos de espera y mejorar el flujo de material.
Algunas empresas líderes están recurriendo a una gama de palancas de la Industria 4.0 para aumentar la productividad, que deben integrarse perfectamente en los sistemas operativos existentes. Entre los más efectivos están estos:
- Los sensores de Internet de las cosas impulsarán la transparencia de OEE y ofrecerán información detallada sobre microparadas, así como pérdidas de OEE que no son evidentes a partir de datos de alto nivel (por ejemplo, pérdidas de OEE no supervisadas/no contabilizadas o entradas defectuosas, como asignación incorrecta de grupos de pérdidas).
- El despacho en tiempo real impulsará las tasas de utilización. Aquí, el software monitorea el material en producción y lo asigna a las máquinas para minimizar los tiempos de espera y maximizar el rendimiento. Mientras tanto, los datos pueden informar la planificación para administrar de manera más efectiva la distribución, enviar material a corredores infrautilizados y evitar el desperdicio.
- El análisis de rendimiento avanzado puede rastrear matrices defectuosas hasta las posiciones de las obleas frontales. Esto se vuelve cada vez más importante para paquetes avanzados, donde los modos de falla eléctrica y térmica son esenciales. También facilitará la introducción gradual de estructuras de transistores avanzadas, incluidos los transistores de efecto de campo (FET) gate-all-around (GAA) y los FET de nanoláminas, que actualmente son resistentes a la detección de defectos convencional debido a su pequeño tamaño y forma tridimensional. .
- El análisis de prueba avanzado eliminaría los bloques de prueba innecesarios, como aquellos con bajas tasas de falla. Esto será cada vez más importante a medida que aumente la complejidad del chip, impulsada por un número cada vez mayor de transistores por chip y una mayor complejidad del paquete. Estos, a su vez, generarían requisitos para tiempos de prueba más largos en equipos de prueba de alto gasto de capital.
- Los vehículos guiados automatizados (AGV) y los robots móviles autónomos (AMR) pueden mejorar el manejo de materiales y agilizar las operaciones en las fábricas back-end totalmente nuevas. Muchas fábricas de campos grises no están configuradas para maximizar su uso. Una razón clave son las limitaciones de espacio y la necesidad de acomodar la cantidad de AGV/AMR requeridos.
- El análisis de video puede optimizar el ensamblaje manual . A diferencia de la fabricación inicial, hay una serie de pasos de inspección visual en la parte trasera que requieren un tiempo significativo del operador. Los ejemplos incluyen la inspección y el mantenimiento de placas quemadas, la inspección de defectos después de la unión de cables y la inspección de moldes. Aquí, la inspección visual automática, impulsada por algoritmos de aprendizaje automático, puede ayudar a optimizar los procesos y reducir la mano de obra.
- La optimización de parámetros de procesos impulsada por análisis , especialmente las pruebas y las pruebas de quemado, a menudo se ve afectada por una operación de controlador subóptima, así como por sitios de prueba defectuosos o inactivos, lo que genera restricciones en el rendimiento. Los análisis avanzados pueden alinear las velocidades del controlador en las flotas de probadores, mientras que los algoritmos de aprendizaje automático en los tableros de prueba pueden predecir fallas en el sitio.
- Algunos fabricantes de back-end ya implementan gemelos digitales (es decir, el modelo virtual de un producto/sistema de producción) en capacidad, mantenimiento y optimización de la cadena de suministro. Una aplicación más poderosa modelaría holísticamente la interacción entre la cadena de suministro, WIP (trabajo en proceso), operadores y máquinas y mantenimiento para identificar problemas de rendimiento, predecir burbujas WIP y ODD (fechas de entrega a tiempo) y acelerar rampas de producción. Un desafío común es la falta de disponibilidad de datos junto con la falta de ciclos de retroalimentación del mundo real.
Sistemas de gestión
En los niveles superiores, un desafío común es una estructura de KPI débil y la recopilación de datos manual o semiautomatizada de sistemas desconectados. Esto conduce a una falta de transparencia y, a menudo, a una acción retrasada. Además, los objetivos de alto nivel no se traducen en objetivos de planta y turnos, lo que refleja una desconexión entre la alta dirección y las operaciones diarias. Por lo general, los operadores de planta no tienen claras las expectativas, lo que lleva a un compromiso limitado y bajas tasas de retención.
¿ Le gustaría aprender más sobre nuestra Práctica de Semiconductores ?
La desconexión se puede mitigar a través de KPI claros y el uso de tableros para supervisión y monitoreo. Estos deben estar indexados a las operaciones diarias del taller (por ejemplo, troqueles producidos o probados por turno y área o rendimiento general por turno). Se deben realizar reuniones periódicas a nivel superior para monitorear los procesos y resolver los cuellos de botella. Cuando no se alcanzan los objetivos, la alta gerencia debe apoyar la resolución de problemas, participar en caminatas Gemba (un enfoque esbelto en el que los gerentes visitan físicamente el piso de producción) y trabajar para eliminar posibles obstáculos. Por el contrario, cuando se alcanzan o superan los objetivos, los logros deben reconocerse y recompensarse, y luego ajustarse para captar las mejoras.
Mentalidades y comportamientos
El cambio organizacional efectivo se basa en la cultura y la mentalidad. Las medidas simples, como las sesiones regulares de retroalimentación, la presentación de los éxitos a los gerentes senior y los módulos de aprendizaje personalizados (por ejemplo, sobre automatización, principios de fabricación y calidad) pueden despertar el entusiasmo y garantizar que la toma de decisiones esté alineada.
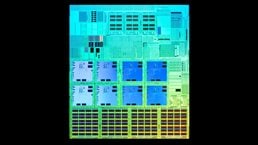
Búsqueda de chips: la solución de adquisición de semiconductores cuando fallan otras opciones
Por lo general, se requiere un cambio en el estilo de liderazgo. Los líderes aplicarán el “Trabajo estándar” del líder, definiendo qué, cuándo y cómo los líderes deben actuar. Esto puede significar, por ejemplo, estar en el piso de producción para recorridos de Gemba y confirmaciones de procesos, apoyar la resolución de problemas de causa raíz y ofrecer retroalimentación y capacitación regulares. Mientras tanto, los gerentes de turno deben trabajar para impulsar la autonomía a nivel de planta y liderar los diálogos de desempeño. Las iniciativas de trabajo en equipo pueden ayudar a forjar un sentido de colaboración y aprendizaje. Al mismo tiempo, un programa personalizado de desarrollo de capacidades en torno a la excelencia en la fabricación y la automatización industrial ayudará a integrar y sostener la transformación.
Finalmente, las empresas no deberían avergonzarse de celebrar sus éxitos. Tiene sentido articular y comunicar la historia del cambio de transformación, abordar la resistencia cultural de frente y mostrar cómo las mejoras en el desempeño personal y operativo van de la mano.
La transformación de las operaciones back-end puede tener un impacto significativo en el rendimiento, la productividad y el rendimiento de la planta, pero el impacto depende de la eficacia de las iniciativas de cambio. Los más exitosos se basan en tres pilares: sistemas operativos, sistemas de gestión y mentalidades y comportamientos. Nuestra experiencia muestra que una combinación de herramientas analíticas y de automatización, una supervisión mejorada y un cambio cultural pueden producir resultados en solo uno o dos meses, mientras que las ganancias de capacidad se acumulan en uno o dos años. Con estos beneficios en mente, los tomadores de decisiones tienen la oportunidad de volver a enfocarse en la ejecución, resolver los cuellos de botella y avanzar hacia una estrategia de back-end más sólida y determinada.
McKinsey